O MTBF (Mean Time Between Failures), que pode ser traduzido como “Tempo Médio entre Falhas” em português, é de fato um dos principais indicadores utilizados na indústria para avaliar a confiabilidade e a qualidade de equipamentos, sistemas ou processos. Ele representa o tempo médio que decorre entre duas falhas consecutivas em um determinado componente ou sistema, ou seja, é uma medida de quanto tempo algo funciona antes de ocorrer uma falha.
O desenvolvimento de um módulo especializado no controle do MTBF pela EGA (presumivelmente uma empresa ou organização) é uma iniciativa valiosa, pois ajuda a monitorar e melhorar a confiabilidade dos equipamentos e processos industriais. Esse módulo provavelmente envolve a coleta de dados relevantes, análise estatística e a geração de relatórios para acompanhar a evolução do MTBF ao longo do tempo.
O que é e como calcular o MTBF
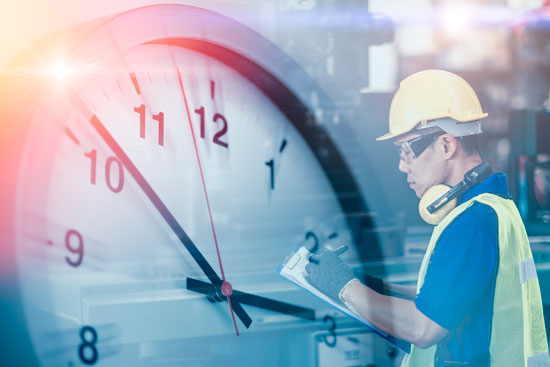
O MTBF (Mean Time Between Failures) ou “Tempo Médio entre Falhas” é uma métrica que expressa a média de tempo que um sistema, equipamento ou componente funciona normalmente antes de ocorrer uma falha. É uma medida de confiabilidade amplamente usada em diferentes setores industriais para avaliar a eficácia e a qualidade de produtos ou processos.
O cálculo envolve alguns passos básicos:
Coleta de dados: Registre o tempo entre falhas de um determinado sistema, equipamento ou componente. Esses dados são normalmente expressos em unidades de tempo, como horas, dias, semanas, etc.7
Cálculo do Tempo Total de Operação (TTO): Some os tempos de operação entre cada falha. Isso fornece a quantidade total de tempo em que o sistema esteve em funcionamento antes de falhar.
Número de Falhas (NF): Conte quantas falhas ocorreram durante o período de observação.
Cálculo: Use a fórmula básica do MTBF para calcular a média de tempo entre falhas:
MTBF = TTO / NF
O resultado dessa fórmula é o tempo médio entre as falhas. Por exemplo, se um equipamento operou por um total de 1000 horas e experimentou 5 falhas durante esse período, o cálculo do MTBF seria:
MTBF = 1000 horas / 5 falhas = 200 horas/falha
Isso significa que, em média, o equipamento funcionou por 200 horas antes de cada falha.
É importante observar que ele é mais eficaz quando usado para avaliar sistemas ou equipamentos que têm uma taxa de falha constante e podem ser reparados após cada falha. Além disso, é fundamental entender que o MTBF não é uma previsão precisa de quando uma falha ocorreu, mas sim uma métrica histórica que fornece informações sobre o desempenho passado.
Em situações onde o sistema tem uma taxa de falha variável ou é complexo, outras métricas de confiabilidade podem ser mais apropriadas, como o MTTF (Mean Time To Failure) ou “Tempo Médio até a Falha”, que lida com sistemas que não podem ser reparados entre falhas, ou a análise de distribuições de probabilidade para modelar os padrões de falha.
Por que é importante ter controle sobre o MTBF e qual a sua relação com a manutenção industrial?
O controle sobre o Tempo Médio entre Falhas é fundamental em ambientes industriais por diversas razões, especialmente em relação à manutenção industrial. Aqui estão alguns motivos pelos quais o controle é importante e como ele se relaciona com a manutenção:
Confiabilidade e eficiência: É uma medida direta da confiabilidade de um sistema ou equipamento. O manter alto indica que o equipamento está funcionando de maneira confiável e com poucas interrupções. Isso leva a uma maior eficiência operacional, pois menos tempo é perdido devido a falhas não programadas.
Planejamento de manutenção preventiva: Quando controlado, permite que as equipes de manutenção industrial programem a manutenção preventiva de forma mais eficaz. Quando o MTBF é conhecido e confiável, é possível agendar paradas de manutenção antes que ocorra uma falha, reduzindo o risco de interrupções não planejadas.
Redução de custos: Equipamentos com MTBF baixo tendem a exigir manutenção corretiva frequente. Isso não apenas causa paradas inesperadas, mas também pode ser mais caro, pois reparos de emergência são geralmente mais dispendiosos do que manutenção planejada. Se controlado permite uma alocação mais eficiente de recursos.
Melhoria contínua: A análise constante pode identificar padrões e tendências nas falhas. Isso pode levar a melhorias contínuas no design, fabricação e manutenção de equipamentos, visando aumentar essa técnica ao longo do tempo.
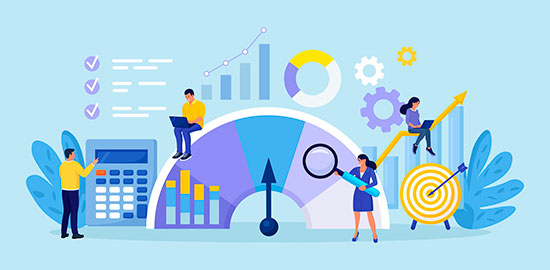
Segurança e qualidade do trabalho: Equipamentos com MTBF baixo podem representar riscos de segurança para os trabalhadores, especialmente em setores perigosos. Além disso, quando as falhas ocorrem com frequência, a qualidade do trabalho pode ser afetada, levando a produtos ou serviços de baixa qualidade.
Aumento da produtividade: Equipamentos mais confiáveis resultam em menos tempo perdido devido a paradas inesperadas, o que aumenta a produtividade geral da operação industrial.
Satisfação do cliente: Equipamentos que funcionam de maneira confiável geralmente levam a um melhor atendimento ao cliente, já que prazos e entregas são mais previsíveis.
O controle é crucial porque está diretamente ligado à confiabilidade, eficiência e qualidade dos equipamentos industriais. Ele desempenha um papel vital no planejamento de manutenção, na otimização de custos e na garantia de operações suaves e seguras, impactando positivamente a produtividade e a satisfação do cliente.
Como o módulo EGA_PCM ajuda a produzir com menor incidência de falhas e consequentemente maior eficiência?
O “Módulo EGA_PCM” é uma ferramenta especializada criada pela EGA para acompanhar e melhorar a confiabilidade e eficiência dos equipamentos e processos industriais, através do monitoramento e análise. Com ele:
Coleta de dados automatizada: O módulo pode automatizar a coleta de dados relacionados às falhas dos equipamentos. Isso pode envolver sensores e sistemas de monitoramento que registram informações sobre tempo de parada e operação.
Análise estatística avançada: O módulo pode realizar análises estatísticas sofisticadas nos dados coletados para identificar padrões de falha, tendências sazonais e outros insights relevantes. Isso ajuda a entender as principais causas das falhas e a tomar medidas para mitigá-las.
Visualizações e relatórios: O módulo pode gerar relatórios detalhados e visualizações gráficas que mostram o desempenho ao longo do tempo, facilitando a identificação de melhorias e áreas problemáticas.
Agendamento de manutenção preventiva: Com base nos dados, o módulo pode auxiliar na programação de manutenções preventivas. Isso significa que as manutenções são realizadas antes que as falhas ocorram, reduzindo o risco de interrupções na produção.
Análise de causa raiz: O módulo pode ajudar a identificar as causas subjacentes das falhas, permitindo que as equipes de manutenção resolvam os problemas fundamentais, em vez de apenas tratar os sintomas.
Otimização de recursos: Ao conhecer os equipamentos com esse sistema mais baixo, a equipe pode direcionar recursos de maneira mais eficiente, concentrando-se nas áreas que mais necessitam de atenção.
Melhoria contínua: Com o tempo, o módulo pode ajudar a avaliar o impacto de iniciativas de melhoria e mudanças de processo, permitindo ajustes com base em dados tangíveis.
Ao implementar esse Módulo da EGA, a empresa pode reduzir a incidência de falhas, minimizar paradas não programadas, melhorar a qualidade dos produtos, otimizar a programação de manutenção e, como resultado, alcançar maior eficiência em suas operações industriais. Isso se traduz em uma produção mais consistente, maior tempo de atividade dos equipamentos e melhor satisfação do cliente.
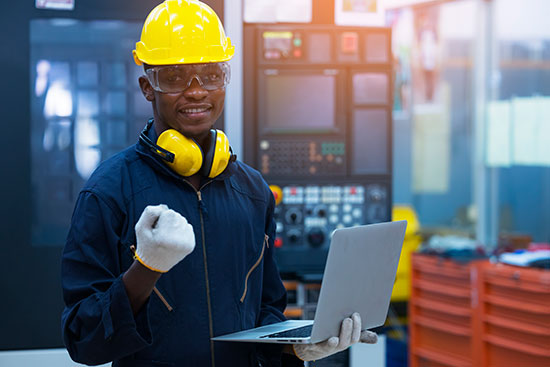
Conte com a EGA!
Se você procura por formas de identificar e eliminar o retrabalho na linha de produção, saiba que a EGA é especialista em fornecer soluções em hardware e software industrial na área de automação, como o sistema MES, integrando todas as informações das máquinas para ter um maior controle de produção. Além disso, tem mais de 30 anos de experiência no mercado de engenharia e automação, que se traduzem em um serviço de excelência que será um diferencial competitivo para a sua empresa, garantindo precisão dos dados para que você consiga implementar um poderoso monitoramento industrial e colaboradores na sua empresa.
A empresa faz a integração de todas as informações das máquinas para ter controle dentro da indústria, trazendo mais eficiência e otimização de recursos e custos por meio da junção de informações de todas as máquinas, viabilizando o monitoramento de produção industrial e processos em tempo real.
Gostou e quer saber mais detalhes? Acompanhe o nosso Blog e não perca nenhuma novidade sobre engenharia e automação! Nos siga em nossas redes sociais: Facebook, Instagram e LinkedIn! Até a próxima!